Safety Management in Organisations
Safety management is the crucial aspects of managerial responsibility to ensure Zero tolerance towards safety in the organizations as any deviation will cost heavily in terms of loss of precious human and economic loss. This can be assured through four pillars of Safety Management which are Safety Policy and Objectives, Safety audit and risk Management, Safety assurance, and safety promotion. But this is not all, one has to look beyond. Recently SpaceX Starship rocket for its Mars mission explode prior to landing at Texas even in spite of taking all precautions of Safety measures, leading to new scope to look beyond. An article by eminent management guru Dr. R D Mishra
Safety management is managing business activities and applying principles, framework, processes to help prevent accidents, injuries and to minimize risk. The objective of a Safety Management System is to provide a structured management approach to control safety risks in operations. Effective safety management must take into account the organization’s specific structures and processes related to safety of operations. There are four pillars or components of an effective safety management system: Viz Policy and objectives, safety risk management, safety assurance, and safety promotion.
- Safety policy and objectives; This first pillar forms the base of an effective safety management system and consists of documentation that lays out the intention of the SMS and the company’s commitment to upholding it. There are four main elements:
- The management commitment: A statement of commitment by the company management to providing the necessary resources, following procedures for reporting incidents, and supplying information to employees where needed. This is agreed to and signed by a responsible executive.
- Safety accountabilities: A document that clearly lays out and defines the responsibilities of various managers and employees at different levels. This should include the appointment of key safety personnel.
- Coordination of emergency response planning.
- SMS documentation. All safety activities should be recorded, and the information made available to employees.
While this pillar includes a lot of paperwork and administration, it’s hugely important as it lays a foundation for the more practical aspects. It’s part of the planning process and should ensure the buy-in of management and employees alike—as well as compliance with local or national regulating bodies. All of this is very important in the highly-regulated construction industry, where a strong top-down culture of safety is critical to a safe site.
2. Safety Audit and risk management; A crucial step to safety is identifying risks to equip those in charge to head off incidents before they happen. This applies not just in aviation but in just about any industry—even an office undergoes risk management to reduce any health and safety risks such as tripping and RSI to an acceptable level. Of course, in an industry like construction which includes some very dangerous roles, safety risk management is essential.
The process starts with hazard identification. On a construction site, this is a tall order! Knowing the hazards, however, is the only way to pre-emptively make things safe for workers—otherwise, safety measures would only be implemented after an accident or near-miss situation. Things to consider in a construction setting include machinery, heights, ladders and scaffolding, vehicles, electricity, flammable materials, exposure to heat and cold… the list is almost endless and will depend on the site and project. Hazards can be assessed according to severity and plans to mitigate risk made around these and incorporated into the SMS program.
- Safety assurance; This pillar is about evaluation—it ensures that the safety management system is constantly being evaluated and adapted to new challenges. The system should be continuously assessed, situational changes addressed, and improvements made according to feedback or audits.
These internal evaluation processes are particularly important on a construction site, where things change and develop as the project progresses. The feedback from workers on the ground is invaluable to a safety management plan, and with good safety management software that allows digital form submission, like Safety Tec’s digital safety forms, it’s easy to collect and collate the necessary information.
Safety assurance also means staying on top of new safety recommendations and regulations from any governing bodies. A safety management plan should include how the organization will respond to these.
4. Safety promotion
Here’s where a concept we have talked about extensively regarding construction safety comes into play: safety culture. This means effective safety communication of all relevant matters to all levels of management and employees, including any changes like the ones mentioned above. This is a two-way street—workers are expected to engage with all safety procedures, encourage others to do so, and provide feedback to management whenever they come across an issue. On a construction site, toolbox talks are a big part of this pillar. When done properly and in an engaging manner, they are a fantastic venue to pass details both ways and keep everyone informed.
Another major part of the safety promotion pillar is safety training and education, a very important undertaking in construction. With a tool like the employee training matrix, safety managers can ensure that workers are achieving and maintaining the necessary or recommended certifications. Training and education are one of the best investments an employer can make in their employees. When it comes to construction safety, training courses can not only up skill people but save lives, too. Continuous improvement of safety practices is best done through a focus on training and education.
While traditionally the four pillars of safety are for aviation service providers, they make a fantastic foundation for safety management in any industry where health and safety is of a particularly large concern—like construction. They lay a solid blueprint for organizational structure and supporting documentation, hazard identification and risk assessment, continued assessment and improvement of safety practices, and a safety culture that includes plenty of training and a free flow of information between all levels of a company.
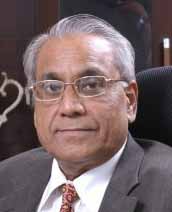
By Dr.R.D.Mishra ,
Director, Greater Noida Productivity Council Frm Director & Head, National Productivity Council, GOI