Quality Management through Six Sigma (6σ)
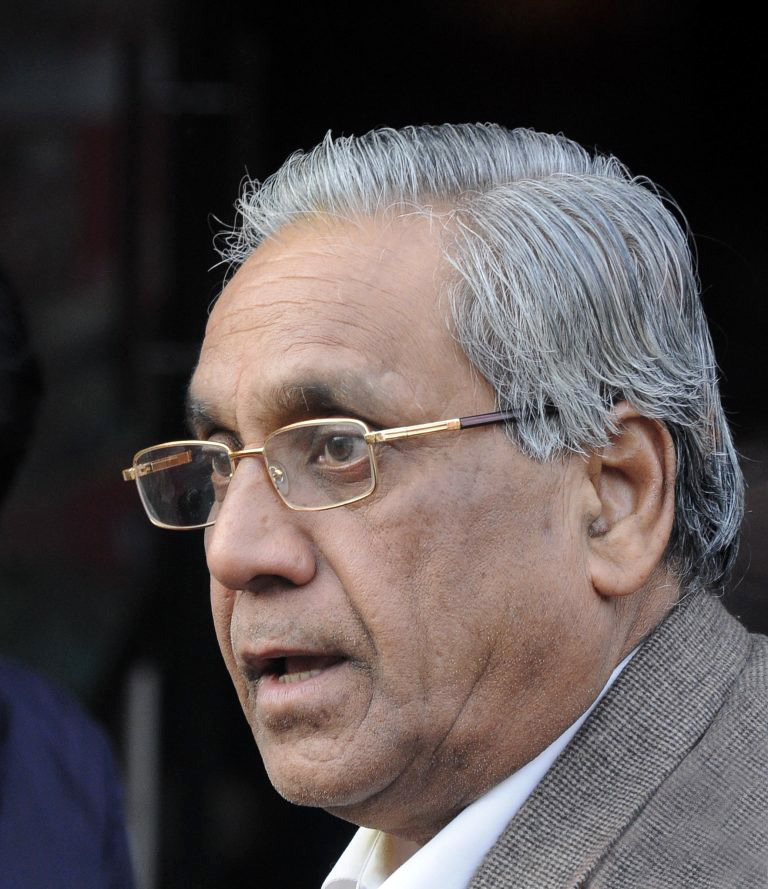
Quality and Productivity is the two sides of the same coin, means without quality, productivity improvement is not possible. National Productivity Council is dedicated for this cause. Quality according to Oxford dictionary “an essential or distinctive characteristic, property, or attribute” The modern definition of quality was given by Mr Joseph Juran a Romanian-born American engineer and management consultant, which is “Meeting or exceeding customer expectations“. Another Management expert W. Edwards Deming defined quality a predictable degree of uniformity and dependability with a quality standard suited to the customer. Therefore Quality is “Conforming to norms” and Quality Management is the act of overseeing all activities and tasks that must be accomplished to maintain a desired level of excellence. This includes the determination of a quality policy, creating and implementing quality planning quality assurance, quality control and quality improvement. Total quality management looks at the bigger picture for quality improvements; it needs consistency of quality processes to maintain customer satisfaction, which can maintain by using the right quality management software solution to streamline and standardize the quality processes in most of the organisations.
Quality is not a program or a discipline. It doesn’t end when you have achieved a particular goal. Quality needs to live in the organization as the “Culture of Quality” in which every person experiences and understands the need for dedication to its values. Employees should think and breathe Quality. It is a continuous process / journey for continuous improvement with no end whatsoever.
Quality Management endeavours to achieve;
- Providing products or service features that customer’s need. These features lead to customer satisfaction and exceeding customer expectations, which, in turn, lead to increased revenue for the producer. Ensuring Quality by adding features that customers want while ensuring consistency and reliability with every iteration has a cost, but the cost of not embracing Quality is much higher, including lost market share, missed opportunities, brand damage, and recalls due to design and manufacturing flaws.
- Designing features that are free from deficiencies and errors. Products or services that are deficient and don’t work as they should require rework or, if they make it to the marketplace, lead to costly recalls and customer dissatisfaction, all of which costs an organization money, time, and brand integrity. Defects found at later stages of product development are far more costly than if they had been found earlier.
- Ensuring ongoing continuous improvement (CI) to address the root causes of defects that are inherent in processes, tools, and designs and that have a significant impact. By addressing the root causes through CI rather than the symptoms, organizations can reduce the Cost of Quality, increase efficiency, sustain a Culture of Quality, minimize rework activities on the shop floor and in the back office, reduce scrap, and ultimately have fewer recall events. Revenue and overall market share then increase as a result of improved product quality, higher levels of customer satisfaction, and increased market share.
“Quality is everyone’s responsibility, but top management have more leverage in their decisions than anyone else down the line.”
Quality Management through Six Sigma (6σ)
The concept of “six sigma” was introduced by American engineer Bill Smith while working at Motorola in 1986. Six Sigma (6σ) is a set of techniques and tools for process improvement. The term “six sigma” comes from statistics and is used in statistical quality control, which evaluates process capability. Processes that operate with “six sigma quality” over the short term are assumed to produce long-term defect levels below 3.4 defects per million opportunities (DPMO).
John Francis Welch Jr. was an American business executive, chemical engineer, Vice Chairman and CEO of General Electric Co in USA made it central to his business strategy. A six sigma process is one in which 99.99966% of all opportunities to produce some feature of a part are statistically expected to be free of defects.
Six Sigma is a set of methods and tools for business process improvement and quality management. Six Sigma aims to improve quality by finding defects, determining their cause, and improving processes to increase the repeatability and accuracy of process results.
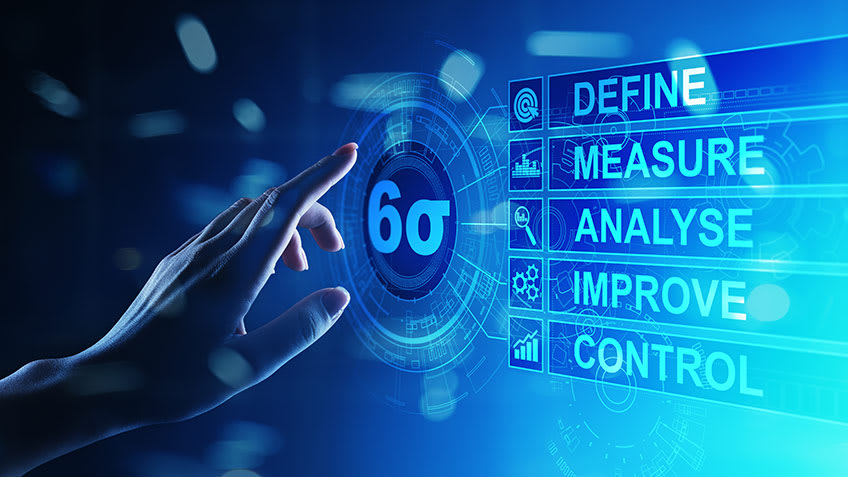
Normal distribution of Six Sigma
Methodologies of Six Sigma;
There are two major methodologies used within Six Sigma, both of which are composed of five sections,
According to “JURAN Institute Six Sigma at Wilton, Connecticut, USA
DMAIC: The DMAIC method is used primarily for improving existing business processes. The letters stand for:
- Define the problem and the project goals
- Measure in detail the various aspects of the current process
- Analyze data to, among other things, find the root defects in a process
- Improve the process
- Control how the process is done in the future
DMADV: The DMADV is another method which is typically used to create new processes and new products or services. The letters stand for:
- Define the project goals
- Measure critical components of the process and the product capabilities
- Analyze the data and develop various designs for the process, eventually picking the best one
- Design and test details of the process
- Verify the design by running simulations and a pilot program, and then handing over the process to the client
Finally to conclude, we have seen Japan, after Second World War emerged as one of the richest economies in the world only by adopting Quality Management and six sigma policies in all its industries and organisations irrespective of nature of product and services offered. Most of the advanced countries in the World have embraced the tool and techniques of Quality Management. It is a potential tool for continuous Improvement in the process of Quality Management, without which it is difficult for India to survive in a fierce competitive world, facing in all walks of life, if we have to fulfil the dream of becoming 5 trillion economies by 2024 from present 3 trillion.